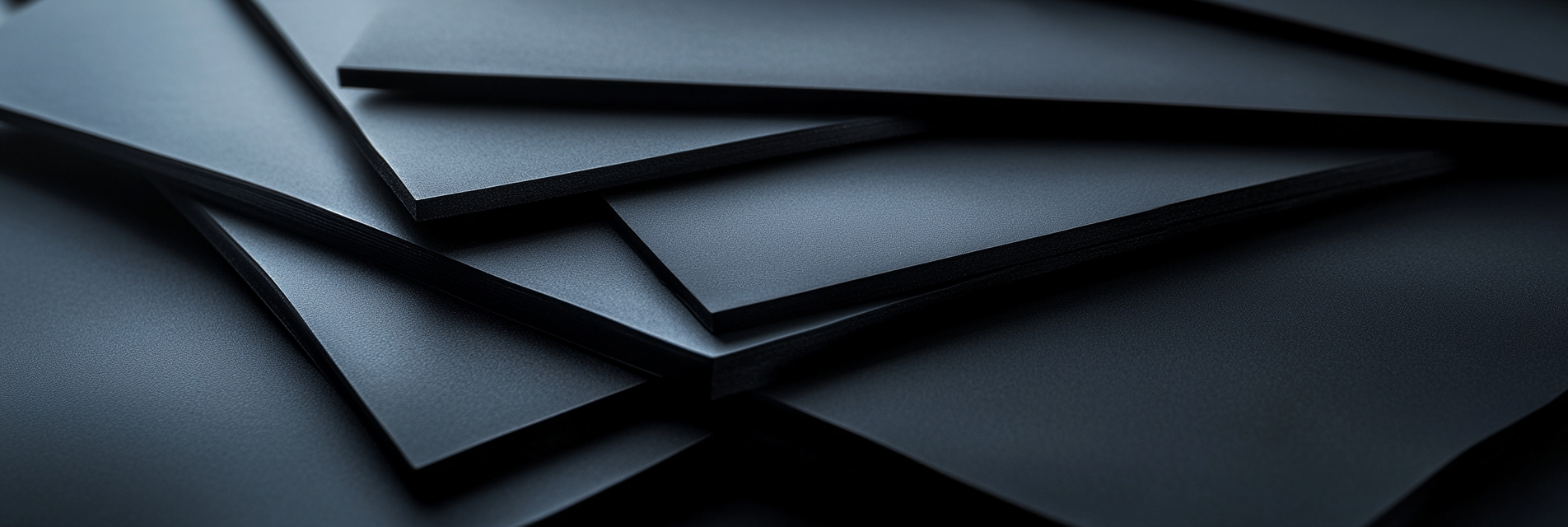
EPDM RUBBER
-
1/32” Thick – 40A Durometer – Commercial Grade Black EPDM Rubber
Regular price From $34.16 USDRegular priceUnit price / per -
1/32" Thick - 50A Durometer - Commercial Grade Black EPDM Rubber
Regular price From $28.02 USDRegular priceUnit price / per -
1/32" Thick - 60A Durometer - Commercial Grade Black EPDM Rubber
Regular price From $25.10 USDRegular priceUnit price / per -
1/32" Thick - 70A Durometer - Commercial Grade Black EPDM Rubber
Regular price From $25.10 USDRegular priceUnit price / per -
1/16" Thick - 40A Durometer - Commercial Grade Black EPDM Rubber
Regular price From $58.23 USDRegular priceUnit price / per -
1/16" Thick - 50A Durometer - Commercial Grade Black EPDM Rubber
Regular price From $40.55 USDRegular priceUnit price / per -
1/16" Thick - 60A Durometer - Commercial Grade Black EPDM Rubber
Regular price From $36.85 USDRegular priceUnit price / per -
1/16" Thick - 70A Durometer - Commercial Grade Black EPDM Rubber
Regular price From $36.85 USDRegular priceUnit price / per -
3/32" Thick - 40A Durometer - Commercial Grade Black EPDM Rubber
Regular price From $87.11 USDRegular priceUnit price / per -
3/32" Thick - 50A Durometer - Commercial Grade Black EPDM Rubber
Regular price From $60.77 USDRegular priceUnit price / per -
3/32" Thick - 60A Durometer - Commercial Grade Black EPDM Rubber
Regular price From $55.45 USDRegular priceUnit price / per -
3/32" Thick - 70A Durometer - Commercial Grade Black EPDM Rubber
Regular price From $55.45 USDRegular priceUnit price / per -
1/8" Thick - 40A Durometer - Commercial Grade Black EPDM Rubber
Regular price From $116.63 USDRegular priceUnit price / per -
1/8" Thick - 50A Durometer - Commercial Grade Black EPDM Rubber
Regular price From $81.11 USDRegular priceUnit price / per -
1/8" Thick - 60A Durometer - Commercial Grade Black EPDM Rubber
Regular price From $73.95 USDRegular priceUnit price / per -
1/8" Thick - 70A Durometer - Commercial Grade Black EPDM Rubber
Regular price From $73.95 USDRegular priceUnit price / per -
3/16" Thick - 40A Durometer - Commercial Grade Black EPDM Rubber
Regular price From $174.67 USDRegular priceUnit price / per -
3/16" Thick - 50A Durometer - Commercial Grade Black EPDM Rubber
Regular price From $121.61 USDRegular priceUnit price / per -
3/16" Thick - 60A Durometer - Commercial Grade Black EPDM Rubber
Regular price From $111.05 USDRegular priceUnit price / per -
3/16" Thick - 70A Durometer - Commercial Grade Black EPDM Rubber
Regular price From $111.05 USDRegular priceUnit price / per -
1/4" Thick - 40A Durometer - Commercial Grade Black EPDM Rubber
Regular price From $232.89 USDRegular priceUnit price / per -
1/4" Thick - 50A Durometer - Commercial Grade Black EPDM Rubber
Regular price From $162.04 USDRegular priceUnit price / per -
1/4" Thick - 60A Durometer - Commercial Grade Black EPDM Rubber
Regular price From $148.25 USDRegular priceUnit price / per -
1/4" Thick - 70A Durometer - Commercial Grade Black EPDM Rubber
Regular price From $148.25 USDRegular priceUnit price / per -
3/8" Thick - 40A Durometer - Commercial Grade Black EPDM Rubber
Regular price From $372.40 USDRegular priceUnit price / per -
3/8" Thick - 50A Durometer - Commercial Grade Black EPDM Rubber
Regular price From $242.99 USDRegular priceUnit price / per -
3/8" Thick - 60A Durometer - Commercial Grade Black EPDM Rubber
Regular price From $222.40 USDRegular priceUnit price / per -
3/8" Thick - 70A Durometer - Commercial Grade Black EPDM Rubber
Regular price From $222.40 USDRegular priceUnit price / per -
1/2" Thick - 40A Durometer - Commercial Grade Black EPDM Rubber
Regular price From $461.98 USDRegular priceUnit price / per -
1/2" Thick - 50A Durometer - Commercial Grade Black EPDM Rubber
Regular price From $321.36 USDRegular priceUnit price / per -
1/2" Thick - 60A Durometer - Commercial Grade Black EPDM Rubber
Regular price From $294.40 USDRegular priceUnit price / per -
1/2" Thick - 70A Durometer - Commercial Grade Black EPDM Rubber
Regular price From $294.40 USDRegular priceUnit price / per -
5/8" Thick - 40A Durometer - Commercial Grade Black EPDM Rubber
Regular price From $577.39 USDRegular priceUnit price / per -
5/8" Thick - 50A Durometer - Commercial Grade Black EPDM Rubber
Regular price From $401.70 USDRegular priceUnit price / per -
5/8" Thick - 60A Durometer - Commercial Grade Black EPDM Rubber
Regular price From $370.59 USDRegular priceUnit price / per -
5/8" Thick - 70A Durometer - Commercial Grade Black EPDM Rubber
Regular price From $371.59 USDRegular priceUnit price / per
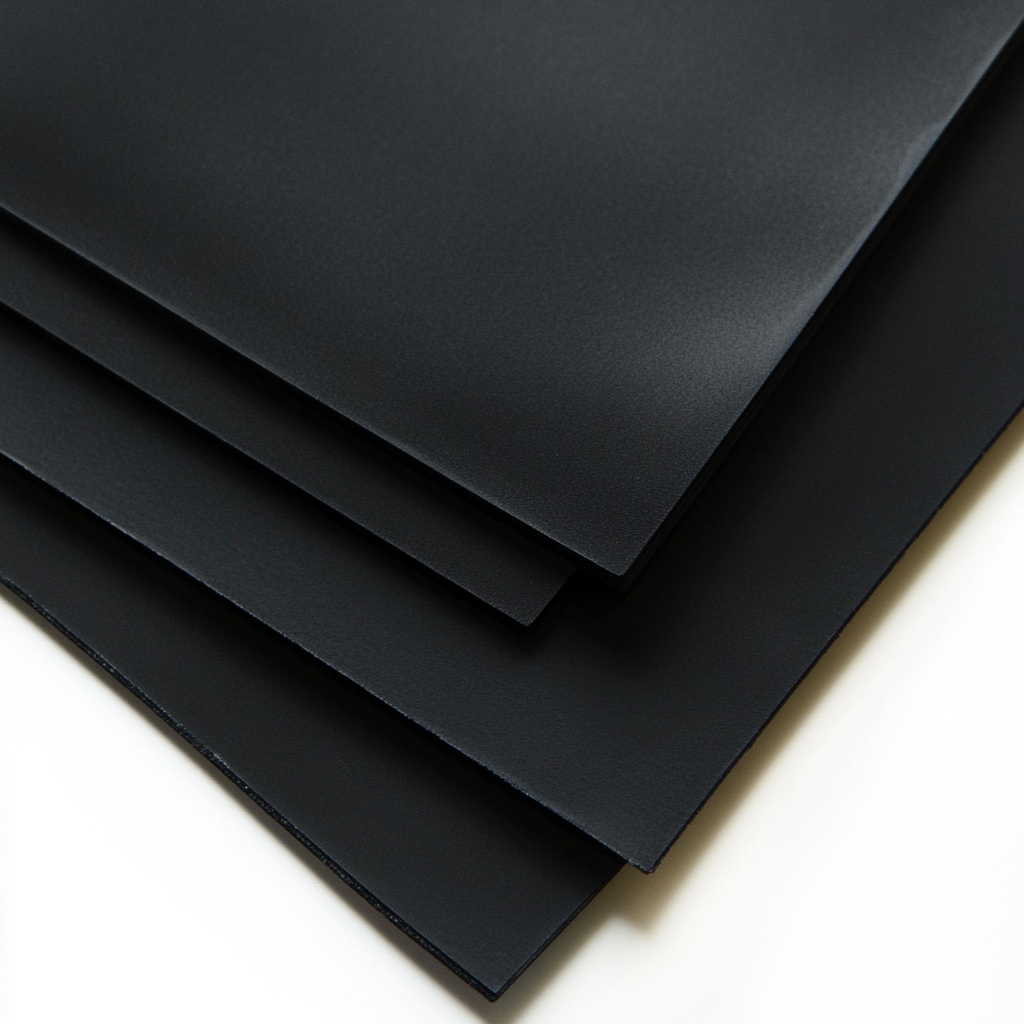
Table of Contents: EPDM Rubber
- EPDM Rubber: The Versatile Ethylene Propylene Diene Monomer Solution
- Superior Properties of EPDM Rubber That Make It Stand Out
- EPDM Rubber Types: Solid, Closed Cell, and Open Cell Options
- EPDM Rubber Sheet Sizes, Thicknesses, and Customization Options
- Versatile Applications for EPDM Rubber Sheets, Gaskets, and Seals
- How to Install EPDM Rubber Sheets: Adhesives and Application Methods
- EPDM Rubber Lifespan: Why Ethylene Propylene Diene Monomer Lasts Decades
- Frequently Asked Questions About EPDM Rubber Sheets, Gaskets, and Applications
EPDM Rubber: The Versatile Ethylene Propylene Diene Monomer Solution
EPDM (Ethylene Propylene Diene Monomer) rubber is a highly versatile synthetic elastomer known for its exceptional durability and weather resistance. As a premium ethylene propylene diene rubber, EPDM maintains its properties under extreme conditions, making it the material of choice for countless industrial, commercial, and residential applications. EPDM rubber combines the strength of ethylene and propylene with the flexibility provided by diene monomers, creating a robust material that withstands environmental challenges where other elastomers fail. Whether you need EPDM rubber sheets, rolls, or gasket material, this remarkable polymer delivers consistent performance in demanding environments.
Browse Additional Gasket Material Options
-
Neoprene Rubber
Neoprene Rubber Shop our neoprene rubber designed for various industrial and residential...
-
Viton® Rubber
Viton® Rubber Viton® Rubber Sheets Viton® Fluoroelastomer Premium Viton® rubber sheets now...
-
PTFE Sheets
PTFE Sheets Our premium PTFE sheets (also known as Teflon sheets) are...
Superior Properties of EPDM Rubber That Make It Stand Out
EPDM rubber (ethylene propylene diene monomer) offers an impressive range of properties that make it ideal for numerous applications:
- Weather Resistance: Exceptional resistance to UV radiation, ozone, and oxygen exposure, preventing degradation even after years in outdoor environments
- Temperature Tolerance: Maintains flexibility and integrity in extreme temperatures from -40°F to +200°F
- Chemical Resistance: Highly resistant to polar substances including water, alcohols, and alkalis
- Moisture Barrier: Low water absorption rate (less than 5%) makes EPDM rubber sheets and seals excellent for waterproofing applications
- Mechanical Strength: High tensile strength with low compression set, allowing EPDM rubber gaskets and seals to maintain their shape under pressure
- Aging Resistance: Unlike many elastomers, EPDM rubber maintains its properties over decades of use
- Electrical Insulation: Excellent dielectric properties make EPDM rubber ideal for electrical applications
These properties make EPDM rubber gasket material and sheets the preferred choice for applications requiring long-term performance in challenging environments.
Comprehensive Rubber Solutions: Beyond EPDM Sheets
-
Gasket Fabrication
Our precision gasket fabrication services transform EPDM and other rubber materials into custom-fit sealing solutions for any application. Using advanced cutting technologies and quality materials, we produce gaskets to your exact specifications with quick turnaround times. From simple washers to complex die-cut shapes, our fabrication capabilities ensure optimal performance and leak-free sealing for your most demanding projects.
-
Rubber Molding
Our rubber molding expertise allows us to create custom EPDM components with exceptional consistency and precision. We utilize compression, transfer, and injection molding techniques to produce complex shapes that maintain tight tolerances and superior performance characteristics. Whether you need small production runs or high-volume manufacturing, our molding capabilities deliver durable rubber parts that perfectly match your engineering requirements.
-
Lathe Cut Ring Gaskets
Our specialized lathe cutting technology produces precise EPDM ring gaskets with exceptional dimensional accuracy and clean edges. These precision-machined seals offer superior performance for critical applications in fluid handling, pressure vessels, and mechanical systems. Available in various cross-sections and diameters, our lathe cut rings provide reliable sealing solutions without the tooling costs associated with molded products.
EPDM Rubber Types: Solid, Closed Cell, and Open Cell Options
EPDM rubber is available in several distinct forms, each engineered for specific performance requirements:
Solid EPDM Rubber Sheets and Rolls
Solid EPDM is a dense, non-porous material offering maximum weather resistance, UV protection, and chemical compatibility. This form of ethylene propylene diene rubber weighs approximately 1lb per sq. ft. in 1/4" thickness and provides superior impermeability to moisture and chemicals. Solid EPDM rubber is ideal for heavy-duty applications requiring maximum durability, such as industrial EPDM gaskets, seals, and weather-resistant barriers.
Closed Cell EPDM Rubber
Closed cell EPDM features sealed air pockets within its structure, making it lightweight (approximately 0.5lbs per sq. ft. in 1/4" thickness) while maintaining excellent water resistance. This structure prevents moisture penetration while providing thermal and acoustic insulation. Closed cell EPDM rubber is perfect for EPDM gasket material in applications requiring compression recovery, such as HVAC systems, automotive weatherstripping, and marine applications.
Open Cell EPDM Rubber
Open cell EPDM contains interconnected air pockets, allowing air and moisture to pass through. While less waterproof than solid or closed cell EPDM, it offers superior breathability and shock absorption. Open cell EPDM rubber is commonly used for cushioning, padding, and sound insulation applications.
Choosing between these EPDM rubber types depends on your specific requirements for durability, insulation, flexibility, and water resistance.
3/16" Thick - 70A Durometer - Commercial Grade Black Neoprene Rubber
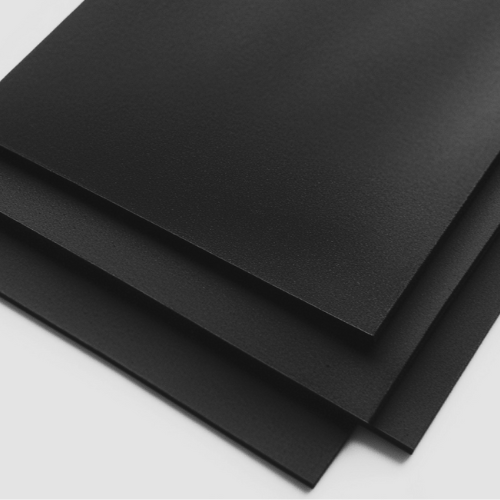

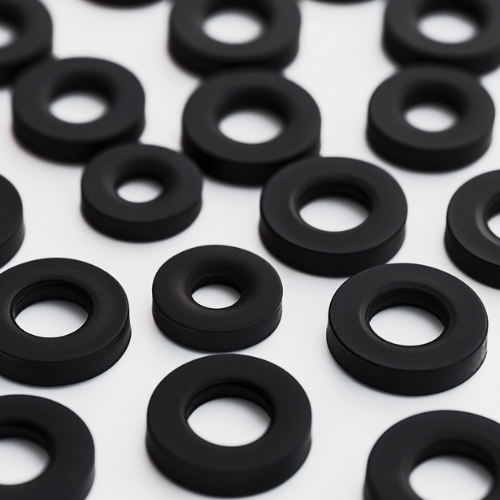

EPDM Rubber Sheet Sizes, Thicknesses, and Customization Options
EPDM rubber sheets are available in various thicknesses and dimensions to meet diverse application requirements:
Solid EPDM Rubber Sheet Thicknesses
Solid EPDM rubber sheets typically range from 1/32" to 1" thick, with standard options including:
- 1/32" - Economical option for thin gaskets and liners
- 1/16" - Popular for general-purpose applications
- 3/32" - Medium thickness for balanced performance
- 1/8" - Standard for many industrial applications
- 3/16" - Enhanced durability for demanding environments
- 1/4" - Heavy-duty applications requiring maximum strength
- 3/8" - Robust solution for high-compression environments
- 1/2" - Excellent for vibration dampening and heavy load applications
- 5/8" - Superior impact absorption for industrial equipment
- 3/4" - High-performance thickness for extreme conditions
- 1" - Maximum thickness offering ultimate durability for specialized industrial uses
Closed Cell EPDM Rubber Sheet Dimensions
Closed cell EPDM sheets commonly come in thicknesses from 1/16" to 1"+ thick, with standard sheet sizes of 36" or 39" width by 72" or 78" length. Custom cuts are available to meet specific requirements.
EPDM Rubber Roll Options
EPDM rubber rolls provide flexibility for covering larger areas and are available in various widths from 36" to 48" with lengths ranging from 5' to 50'.
Commercial and Industrial Grades
From commercial-grade EPDM (60A durometer) to specialized formulations, our EPDM rubber sheets and rolls are available in multiple hardness levels to match your application's requirements.
The cost of EPDM rubber sheets varies based on thickness, with thicker sheets providing enhanced durability and impact resistance at a higher price point.
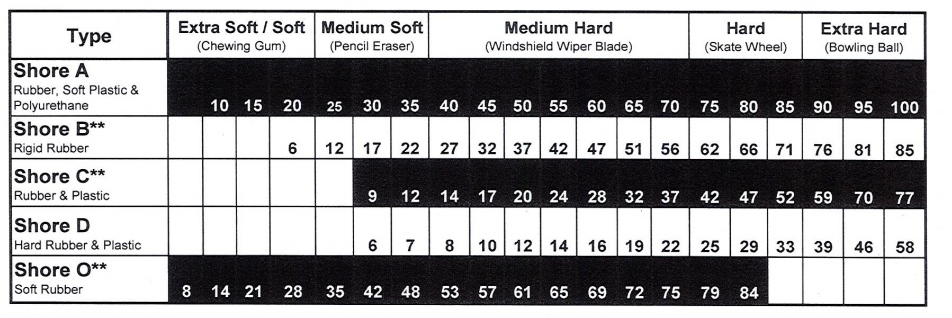
Versatile Applications for EPDM Rubber Sheets, Gaskets, and Seals
Ethylene propylene diene rubber (EPDM) excels across numerous industries due to its exceptional properties:
Industrial Applications
- EPDM Gaskets and Seals: Created from EPDM gasket material, these components provide reliable sealing in manufacturing equipment, preventing leaks even under harsh conditions
- Vibration Isolation: EPDM rubber's flexibility makes it ideal for reducing equipment vibration
- Electrical Insulation: The dielectric properties of EPDM rubber sheets make them excellent for electrical applications
Construction and Roofing
- Waterproofing Membranes: EPDM rubber sheets provide long-lasting water barriers for roofing systems
- Foundation Sealing: EPDM seals protect foundations from water infiltration
- Window and Door Seals: EPDM rubber seals create weather-tight barriers against air and moisture
Automotive Applications
- Weather Stripping: EPDM rubber seals for doors and windows resist UV degradation
- Hoses and Belts: EPDM's temperature resistance makes it ideal for engine components
- Gaskets: EPDM rubber gaskets maintain seals despite temperature fluctuations
HVAC Systems
- Duct Sealing: EPDM gasket material ensures air-tight connections
- Insulation: Closed cell EPDM provides thermal insulation for efficiency
- Vibration Dampening: EPDM rubber isolates mechanical vibrations
Marine Applications
- Hatch Seals: EPDM rubber seals maintain waterproof barriers
- Dock Bumpers: EPDM's durability protects vessels and structures
- Underwater Applications: EPDM's resistance to water and marine growth provides lasting protection
From white EPDM options for specialized applications to standard black EPDM rubber rolls, the material's versatility makes it indispensable across numerous industries requiring durable, weather-resistant elastomers.
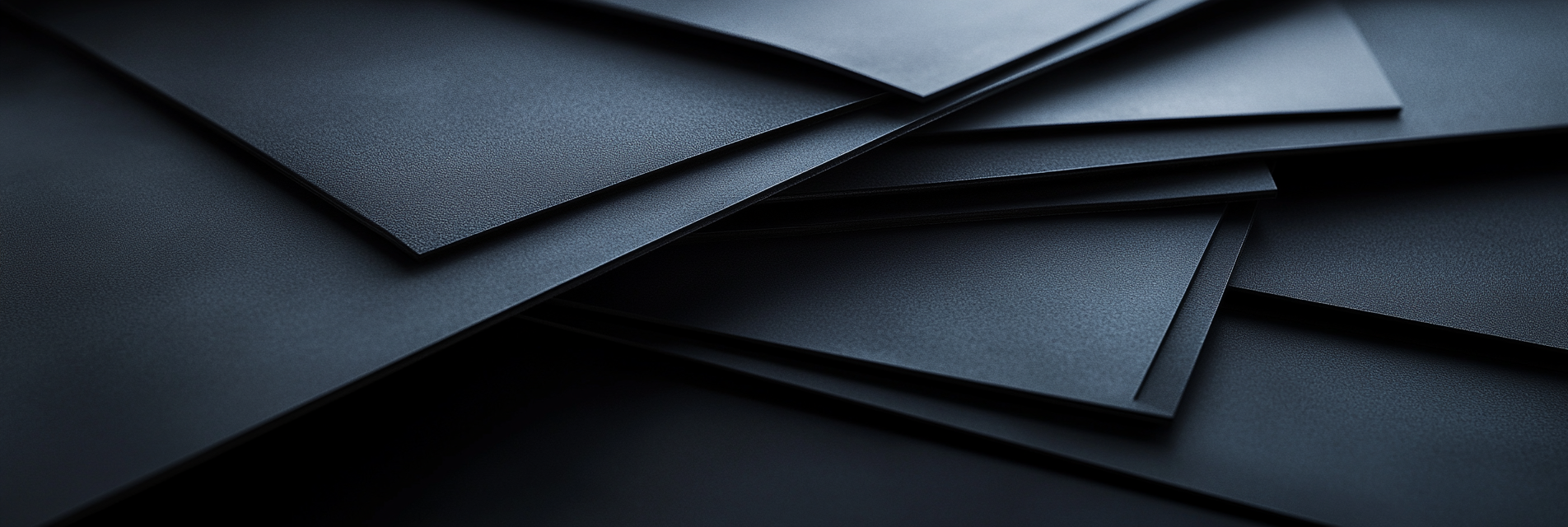
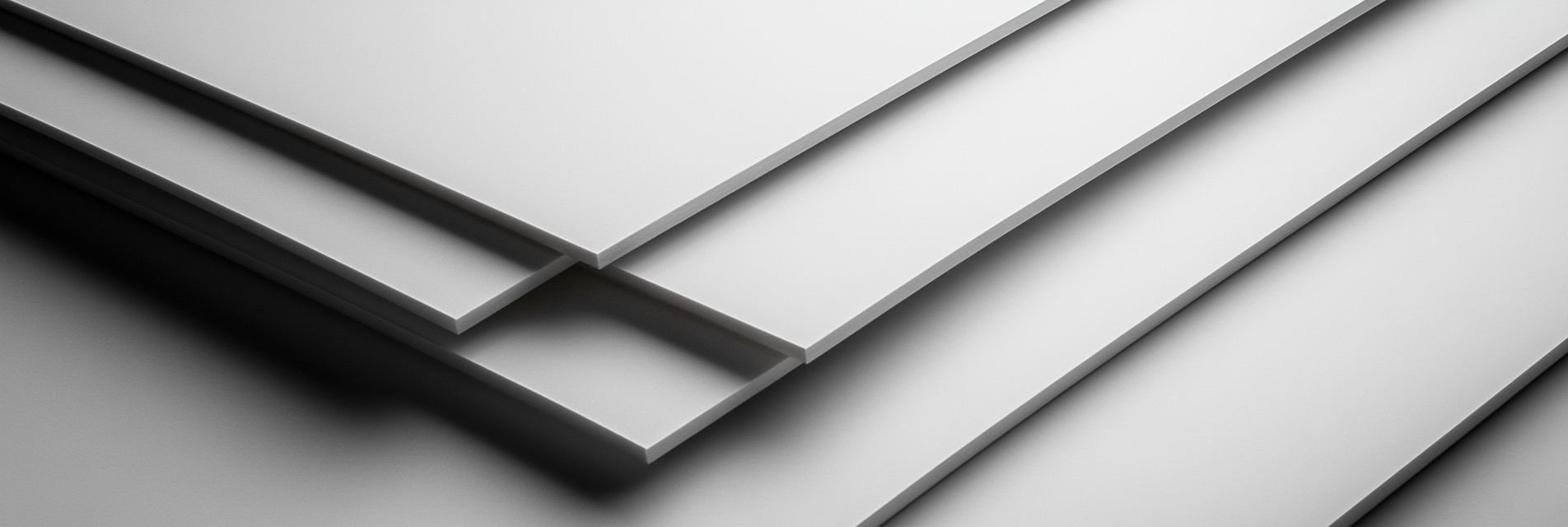
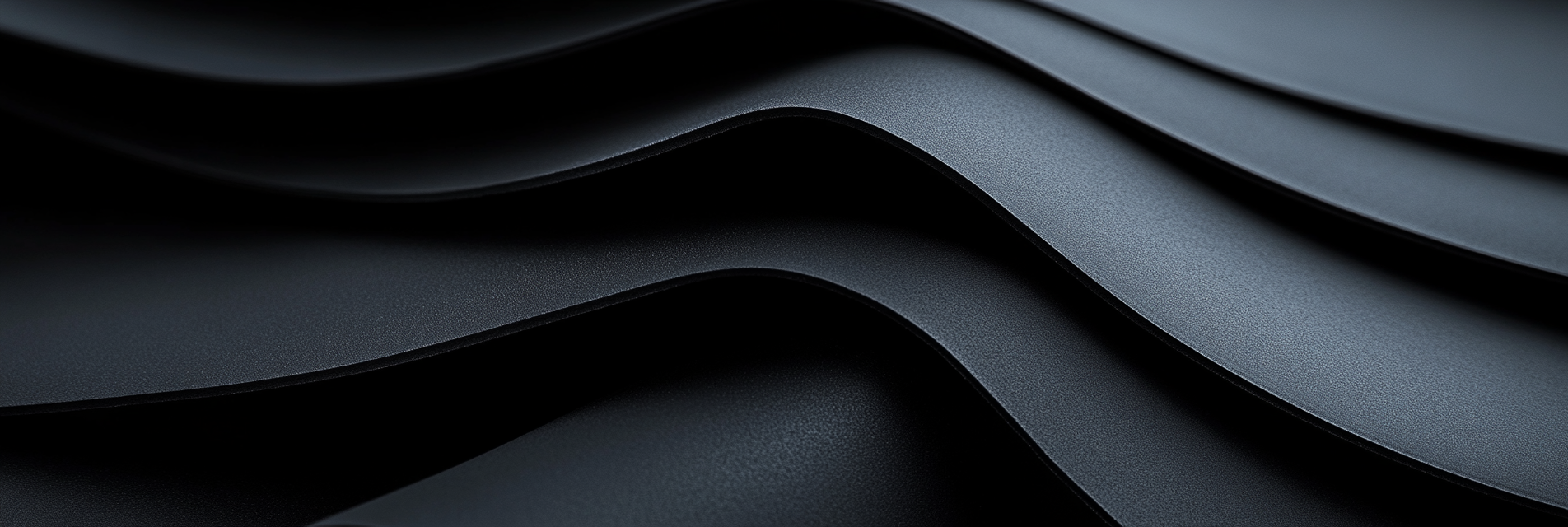
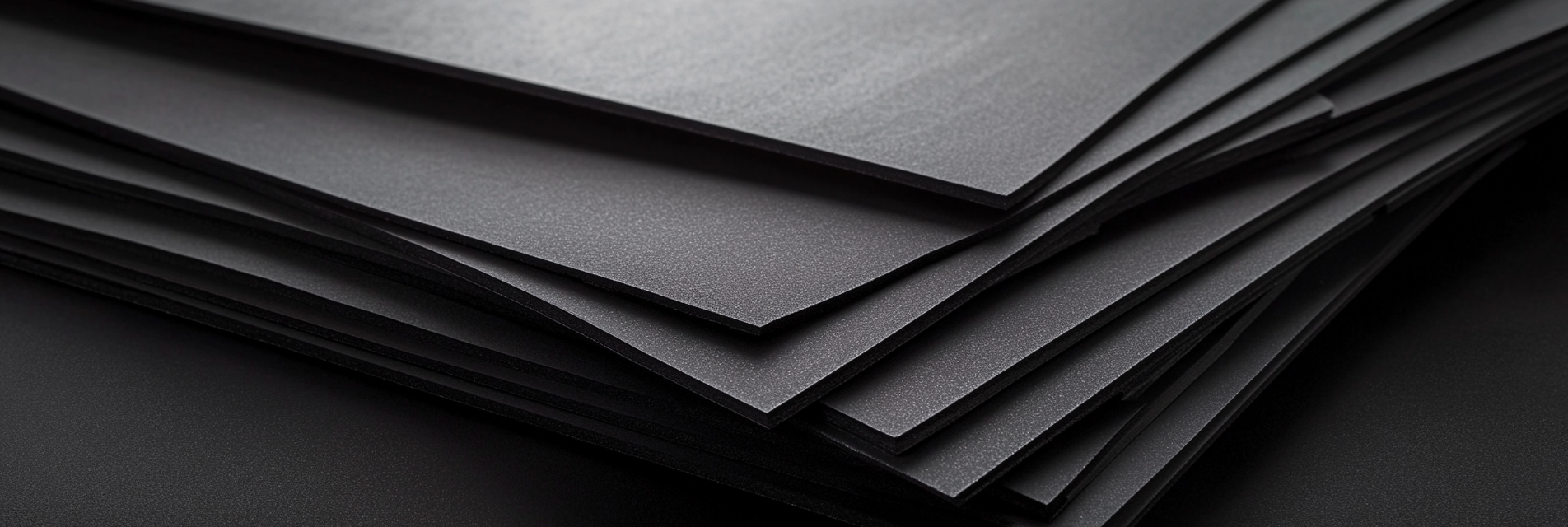
How to Install EPDM Rubber Sheets: Adhesives and Application Methods
Proper installation of EPDM rubber sheets and gaskets ensures optimal performance and longevity:
Recommended Adhesives for EPDM Rubber
For permanent bonding of EPDM rubber, polyurethane-based adhesives provide the best combination of strength and flexibility. Unlike some adhesives that can degrade elastomers, polyurethane formulations create a chemical bond with the ethylene propylene diene structure while maintaining the flexibility needed for rubber applications.
Installation Process for EPDM Rubber Sheets
- Surface Preparation: Clean all surfaces thoroughly to remove dust, oils, and contaminants
- Measuring and Cutting: Cut EPDM rubber sheets slightly larger than required dimensions to allow for positioning
- Adhesive Application: Apply polyurethane adhesive evenly to both the substrate and EPDM rubber
- Bonding: Press the EPDM rubber sheet firmly onto the prepared surface, working from the center outward to eliminate air pockets
- Curing: Allow the recommended curing time before subjecting the bond to stress or environmental exposure
Creating EPDM Rubber Gaskets
When fabricating EPDM gaskets from sheet material:
- Create precise templates based on required dimensions
- Cut EPDM rubber gasket material using appropriate tools (die cutters provide the cleanest edges)
- Verify gasket dimensions before installation
- Install using compression techniques or appropriate adhesives depending on the application
EPDM Rubber Seals Installation
For EPDM rubber seals in automotive or construction applications:
- Ensure proper fit by measuring the gap precisely
- Select appropriate EPDM seal profile (D-shape, P-shape, etc.)
- Use specialized adhesives or mechanical fastening as appropriate
- Test seal integrity before finalizing installation
Proper installation techniques maximize the performance and lifespan of EPDM rubber products in all applications.
The Rubber Blog: Tips, Trends & Technical Insights
View all-
Why Reshoring Rubber Molding to the U.S. Makes ...
Recent tariff changes are reshaping the economics of rubber component sourcing for American manufacturers. With import duties on foreign-made rubber molded products increasing by 25-35%, the cost advantage of overseas...
Why Reshoring Rubber Molding to the U.S. Makes ...
Recent tariff changes are reshaping the economics of rubber component sourcing for American manufacturers. With import duties on foreign-made rubber molded products increasing by 25-35%, the cost advantage of overseas...
-
What is Encapsulation Rubber Molding? A Complet...
This comprehensive guide explains encapsulation rubber molding (overmolding), a multi-step injection molding process where elastomeric materials are molded over existing substrates to create unified components with enhanced properties. The post...
What is Encapsulation Rubber Molding? A Complet...
This comprehensive guide explains encapsulation rubber molding (overmolding), a multi-step injection molding process where elastomeric materials are molded over existing substrates to create unified components with enhanced properties. The post...
-
The Ultimate Guide to PTFE Sheet Types: Which O...
PTFE Sheet Types: PTFE (Polytetrafluoroethylene) sheets, commonly known as Teflon, come in several specialized varieties to meet different industrial needs. Each type offers unique benefits based on manufacturing process and...
The Ultimate Guide to PTFE Sheet Types: Which O...
PTFE Sheet Types: PTFE (Polytetrafluoroethylene) sheets, commonly known as Teflon, come in several specialized varieties to meet different industrial needs. Each type offers unique benefits based on manufacturing process and...
EPDM Rubber Lifespan: Why Ethylene Propylene Diene Monomer Lasts Decades
The exceptional longevity of EPDM rubber makes it a cost-effective choice for long-term applications:
Expected Lifespan of EPDM Rubber
When properly installed and maintained, EPDM rubber products typically last:
- 20-50 years for EPDM rubber seals in automotive applications
- 25-40 years for EPDM rubber roofing membranes
- 30+ years for industrial EPDM gaskets in controlled environments
This remarkable durability stems from the inherent properties of ethylene propylene diene rubber's molecular structure.
Factors Affecting EPDM Rubber Longevity
Several factors influence how long EPDM rubber sheets and products will maintain their performance:
- UV Exposure: Despite excellent resistance, prolonged direct sunlight can eventually affect surface properties
- Temperature Cycling: While EPDM withstands -40°F to +200°F, extreme cycling may impact lifespan
- Chemical Exposure: Concentrated exposure to oils and hydrocarbons can reduce service life
- Mechanical Stress: Constant compression or tension beyond design parameters may affect longevity
Maintaining EPDM Rubber Products
To maximize the lifespan of EPDM rubber:
- Regularly inspect for signs of wear or damage
- Clean with mild soap and water, avoiding petroleum-based cleaners
- Protect from unnecessary exposure to oils and solvents
- Ensure proper installation to prevent undue stress
The exceptional durability of EPDM rubber gaskets, sheets, and seals provides outstanding value over time, with minimal maintenance requirements throughout decades of service.
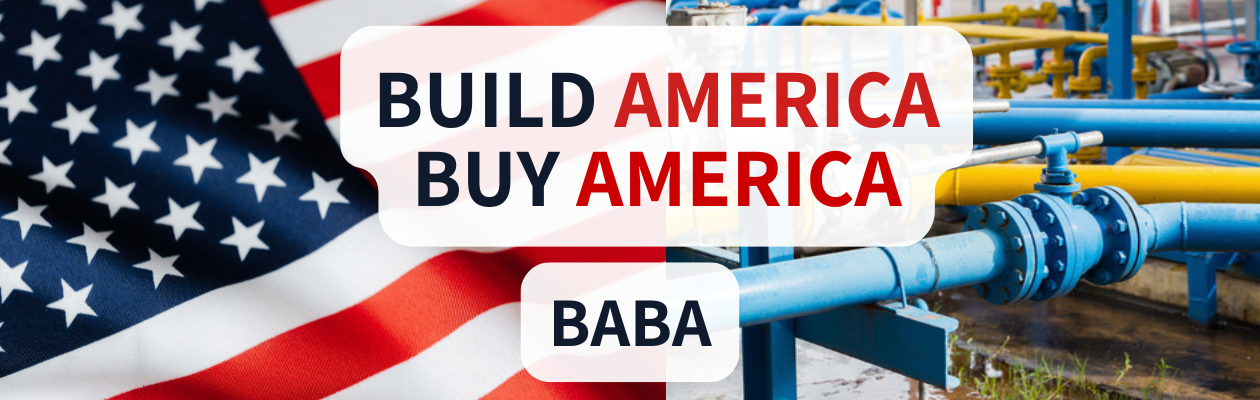