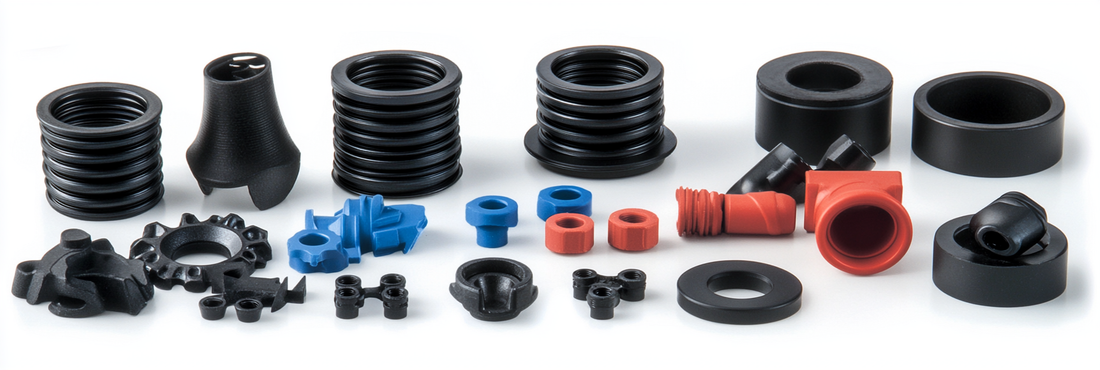
What is Encapsulation Rubber Molding? A Complete Guide to Overmolding
Share
In today's manufacturing landscape, protecting sensitive components from environmental factors while maintaining functionality is critical to product success. Encapsulation rubber molding, also known as overmolding, has emerged as a key manufacturing process that helps companies create more durable, functional, and attractive products. This technique is revolutionizing industries from consumer electronics to automotive and medical devices, offering both protective and aesthetic benefits.
In this post, we'll define encapsulation rubber molding, explain how it differs from other molding processes, showcase real-world applications, and provide best practices for implementing this technology in your next product design.
What is Encapsulation Rubber Molding?
Encapsulation rubber molding, or overmolding, is a multi-step injection molding process where a layer of elastomeric material (typically rubber or thermoplastic elastomer) is molded over an existing substrate or insert. The rubber material chemically bonds or mechanically locks with the substrate, creating a unified part with combined properties of both materials.
This manufacturing technique creates a protective seal around components, enhancing durability while providing benefits like improved grip, vibration dampening, electrical insulation, chemical resistance, and aesthetic appeal. Overmolding allows manufacturers to combine rigid and flexible materials in a single component, eliminating assembly steps and creating more ergonomic, weather-resistant products.
Why is Encapsulation Rubber Molding Important?
Encapsulation rubber molding has transformed modern manufacturing by solving numerous design challenges that traditional manufacturing methods struggle to address. Here's why it matters:
- Enhanced Product Performance: According to a 2023 manufacturing industry report, products utilizing overmolding technology demonstrate a 40% increase in durability and lifespan compared to conventionally manufactured alternatives.
- Cost Reduction: Overmolding can reduce assembly costs by up to 25% by replacing multiple components with a single molded part, as noted by the Manufacturing Technology Association.
- Competitive Advantage: With consumers increasingly valuing ergonomics and durability, overmolded products command higher market prices and customer loyalty. A recent market survey found that 68% of consumers were willing to pay more for products with "soft-touch" components.
- Sustainability: By creating stronger bonds between components, overmolded products typically have longer lifespans and reduced warranty claims, contributing to less waste and lower environmental impact.
As manufacturing moves toward more integrated and efficient processes, mastering encapsulation technology has become essential for companies looking to stay ahead in both functionality and design.
Real Examples of Encapsulation Rubber Molding
1. Consumer Electronics
Modern smartphones and tablets use overmolding to create protective cases with rigid internal frames and soft, shock-absorbing external layers. These cases provide superior drop protection while maintaining a comfortable grip. Similarly, many remote controls feature hard plastic bodies with soft rubber buttons that are overmolded to create better tactile feedback and water resistance.
2. Automotive Applications
The automotive industry extensively uses encapsulation rubber molding for components like gear shifters, dashboard controls, and steering wheels. These parts combine rigid structural elements with soft-touch grips that enhance driver comfort and control. Additionally, under-hood electronic components are frequently overmolded with silicone rubber to protect sensitive electronics from heat, vibration, and moisture.
3. Medical Devices
Medical equipment manufacturers rely on overmolding to create surgical tools with comfortable, non-slip handles that can withstand sterilization processes. Diagnostic equipment often features overmolded seals to prevent fluid ingress while maintaining precise functionality. The biocompatible rubber materials used in these applications ensure patient safety while providing necessary performance characteristics.
4. Industrial Tools
Professional-grade power tools utilize overmolding to create ergonomic handles that reduce user fatigue and provide vibration dampening. The rigid internal structure ensures durability and precise alignment of mechanical components, while the overmolded rubber exterior provides comfort during extended use and protection against drops.
5 Tips and Reminders for Encapsulation Rubber Molding
1. Material Compatibility is Critical
Ensure your substrate and overmold materials are chemically compatible to achieve proper adhesion. Some combinations naturally bond well, while others may require special treatments or bonding agents. Work with material specialists to select the optimal combination for your specific application.
2. Design for Manufacturability
Create designs that account for the specific requirements of the overmolding process. Include appropriate draft angles, wall thickness transitions, and gate locations. Remember that overmolding typically requires more complex tooling than single-material molding.
3. Consider Thermal Properties
Different materials expand and contract at different rates with temperature changes. These coefficient of thermal expansion (CTE) differences can cause stress at the interface between materials. Account for this in your design to prevent warping or separation over time.
4. Balance Hardness Properties
One of overmolding's key advantages is combining hard and soft materials. When selecting your durometer (hardness) values, consider the functional requirements of your part. Too soft may compromise durability, while too hard may negate the ergonomic benefits.
5. Prototype Before Full Production
The interaction between multiple materials can sometimes yield unexpected results. Create prototypes to test functional performance, material bonding, and aesthetic appeal before committing to full production runs.
Closing
Encapsulation rubber molding represents a significant advancement in manufacturing technology, offering designers and engineers unprecedented flexibility in creating products that are both highly functional and user-friendly. By combining the structural integrity of rigid materials with the protective and ergonomic benefits of elastomers, overmolding enables the creation of superior products across virtually every industry.
At Modern Rubber Products, we understand that successful encapsulation molding begins with proper surface preparation. That's why we've invested in a specialized dip line that allows us to coat metal castings or internal components with adhesives and primers before the molding process. This critical step ensures optimal bonding between the substrate and rubber materials, significantly enhancing product durability and performance while reducing the risk of delamination.
As material science continues to advance, we can expect even more innovative applications of this versatile manufacturing process. Whether you're designing consumer electronics, medical devices, automotive components, or industrial tools, understanding and leveraging encapsulation rubber molding—with proper bonding preparation—can give your products a competitive edge in both performance and user experience.
Ready to Elevate Your Product Design with Overmolding?
Contact Modern Rubber Products today for a consultation on how encapsulation rubber molding can enhance your next project. Our team of engineering specialists can help you select the right materials, optimize your design for manufacturability, and deliver high-quality overmolded components that exceed your expectations.