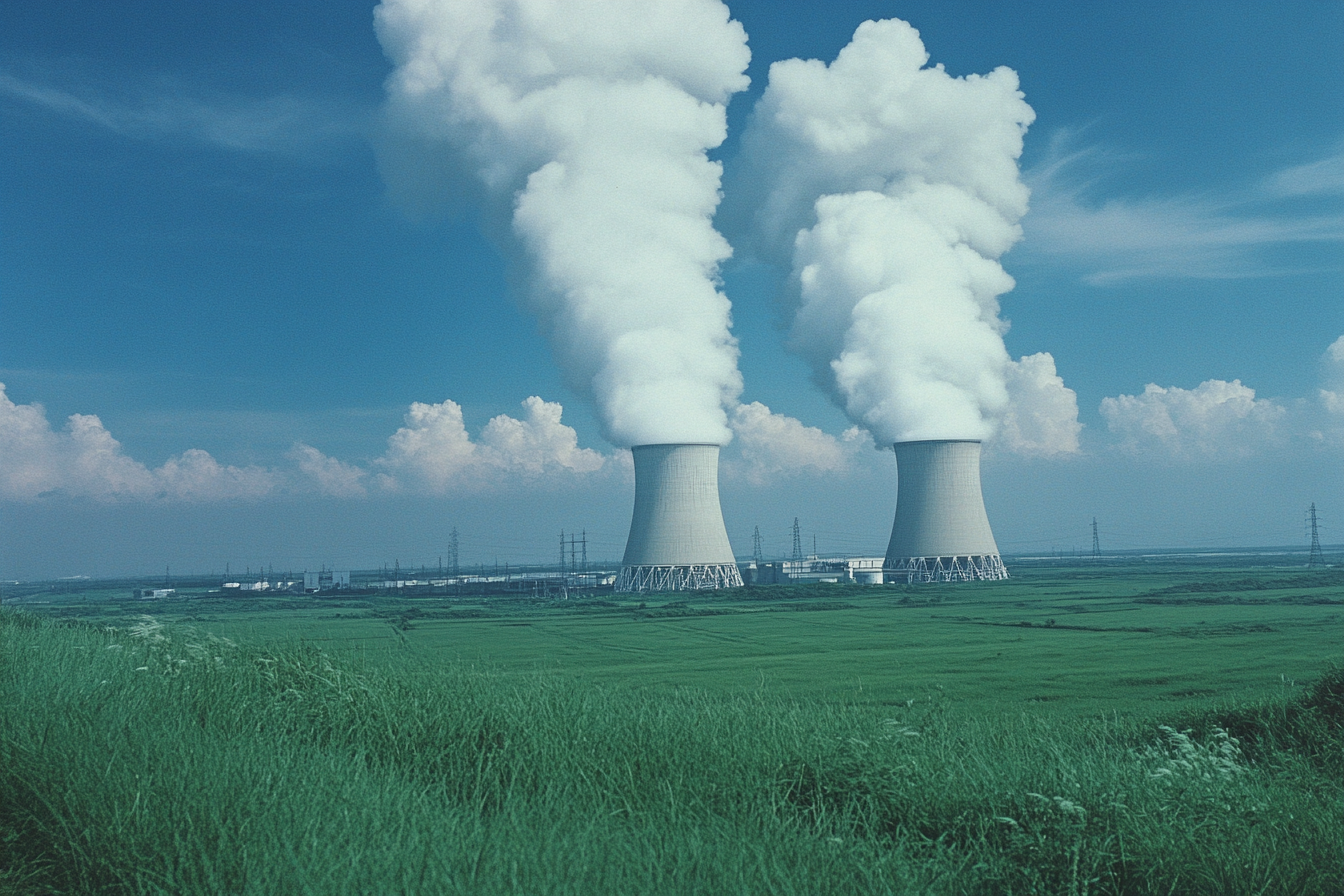
POWER GENERATION INDUSTRY
Power Generation Industry Solutions
Modern Rubber Products delivers specialized sealing components engineered for the extreme demands of power generation facilities. Our high-performance gaskets, seals, and custom rubber components withstand the intense temperatures, pressures, and operational stresses encountered in electrical power production. We provide reliable rubber solutions for conventional fossil fuel plants, nuclear facilities, hydroelectric generators, and renewable energy systems. Our Chattanooga manufacturing facility utilizes advanced materials and precision fabrication techniques to produce components that ensure system integrity, prevent energy losses, and support regulatory compliance while maximizing operational efficiency and minimizing downtime in critical power infrastructure.
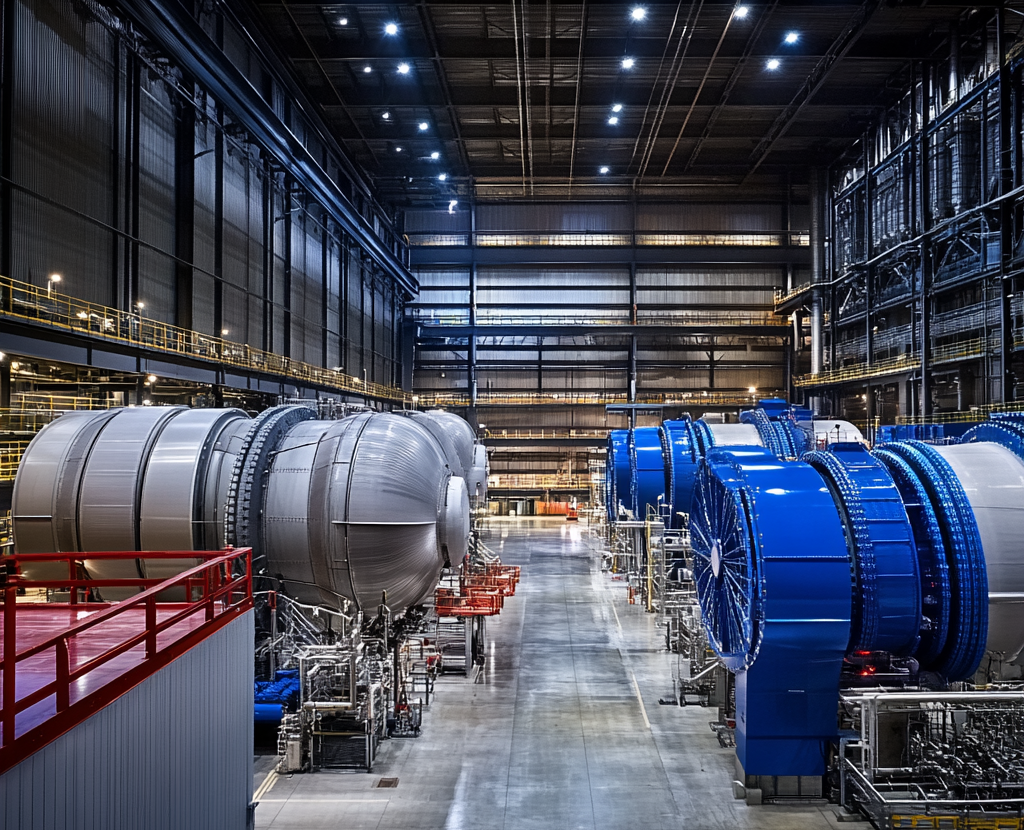
Critical Power Generation Applications
Our rubber components serve essential functions throughout power generation facilities, including:
- High-temperature turbine gaskets and seals
- Steam line expansion joints and flexible connectors
- Cooling water system seals and pump components
- Generator insulation components and vibration dampeners
- Condenser tube sheet gaskets and water box seals
- Valve stem packing and seat seals for steam systems
- Custom fabricated components for emissions control equipment
- Specialized seals for nuclear containment applications
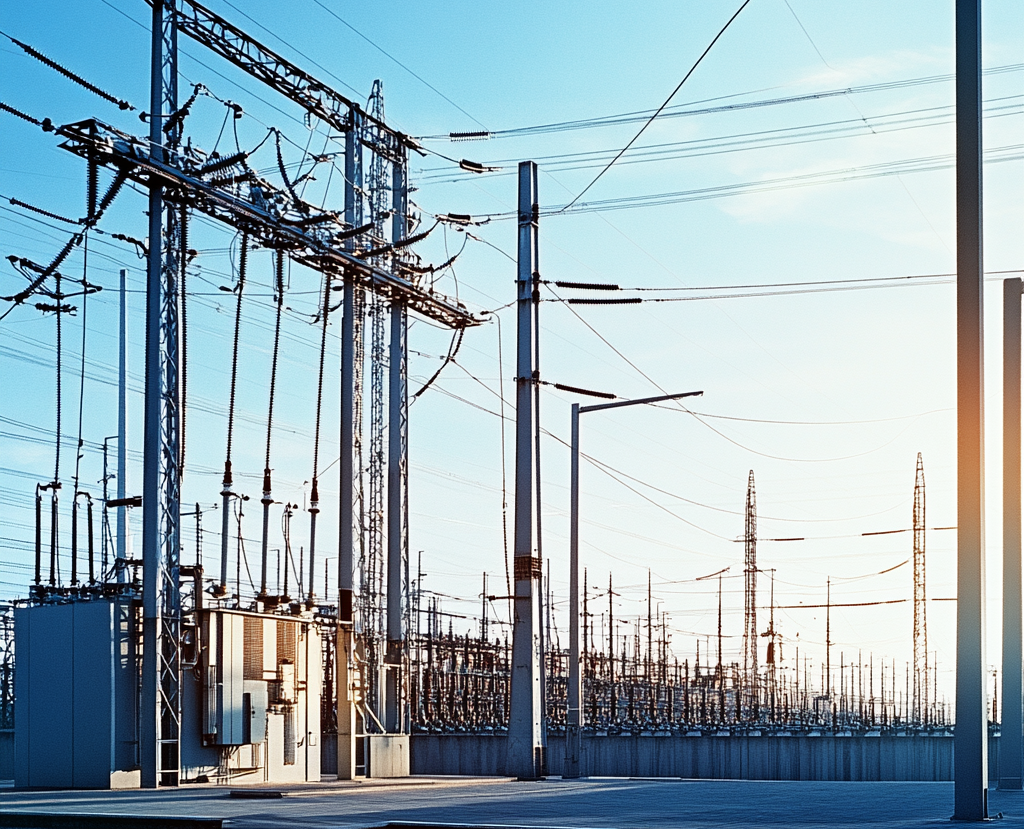
Rubber Engineered for Power System Performance
Modern Rubber Products manufactures a comprehensive range of sealing solutions specifically designed for power generation environments. Our components are produced using materials selected for their documented performance under extreme conditions, ensuring reliability in high-temperature steam systems, cooling water applications, and specialized power plant equipment. We utilize advanced elastomers including EPDM, fluoroelastomers (FKM), silicone, and specialized compounds formulated to withstand radiation, steam exposure, and thermal cycling. Our engineering team ensures each component complies with relevant industry standards while delivering dependable performance in critical power generation systems.
Meeting the Unique Challenges of Power Production
Power generation applications present some of the most demanding environments for rubber components, requiring materials and designs that ensure both operational reliability and safety. At Modern Rubber Products, we understand these specialized needs:
Material Selection for Extreme Environments
Power plant integrity depends on rubber components that maintain their properties despite harsh operating conditions. Our power industry products are manufactured using compounds specifically formulated to withstand:
- Extreme temperatures in steam and exhaust systems
- Continuous hot water and steam exposure
- Radiation exposure in nuclear applications
- Ozone generated by electrical equipment
- Chemical exposure from water treatment systems
Precision Manufacturing for Critical Systems
Power generation components must provide reliable sealing in systems where failure is not an option. Our manufacturing capabilities, including compression molding and waterjet cutting, produce components with exact specifications and tolerances required for proper installation in turbine systems, boiler connections, condenser assemblies, and cooling water applications.
Durability for Continuous Operations
Power plant rubber components must perform reliably in facilities that operate continuously with limited maintenance windows. Our solutions are engineered for exceptional longevity with properties including:
- Excellent compression set resistance for maintained sealing
- Temperature stability across operational ranges
- Resistance to hardening and cracking under thermal cycling
- Low water absorption and excellent dimensional stability
- Compatibility with common power plant chemicals
Specialized Solutions for Renewable Energy Systems
Modern Rubber Products supports the growing renewable energy sector with specialized components for hydroelectric, solar thermal, geothermal, and biomass power generation systems. Our engineering team works with renewable energy equipment manufacturers and facility operators to develop custom sealing solutions that address the unique challenges of these specialized applications, including:
- Hydroelectric turbine seals and wicket gate components
- Concentrated solar power (CSP) high-temperature transfer fluid seals
- Geothermal brine-resistant expansion joints and pipe seals
- Biomass boiler door seals and gasketing systems
Each renewable energy component is manufactured with materials specifically selected for the unique environmental conditions and operational parameters of these sustainable power systems.
Power Generation Industry FAQs
What rubber materials are best suited for high-temperature steam applications?
For high-temperature steam applications, we typically recommend advanced fluoroelastomers (FKM) and certain silicone formulations specifically designed for steam exposure. These materials maintain their sealing integrity at temperatures up to 450°F in continuous service, with specialized compounds available for even higher temperature extremes. For the highest temperature applications, we can provide solutions combining elastomers with high-temperature fabrics or metal reinforcement.
What is the typical lead time for power generation components?
For standard power plant gaskets and seals, we can typically fulfill orders within 1-2 weeks. Components requiring specialized high-temperature compounds may require 2-3 weeks. Custom molded components for unique applications require additional time for tooling development, with typical lead times of 8-10 weeks for initial production. We understand the critical nature of power plant operations and can expedite orders for emergency maintenance situations.
Do you offer solutions for cooling tower and condenser applications?
Yes, we provide a complete range of rubber components specifically designed for cooling water systems, including condenser tube sheet gaskets, expansion joints, and cooling tower fill support components. These products are formulated to resist the biological fouling, chlorine exposure, and continuous wet conditions found in cooling systems while maintaining mechanical properties for years of reliable service.