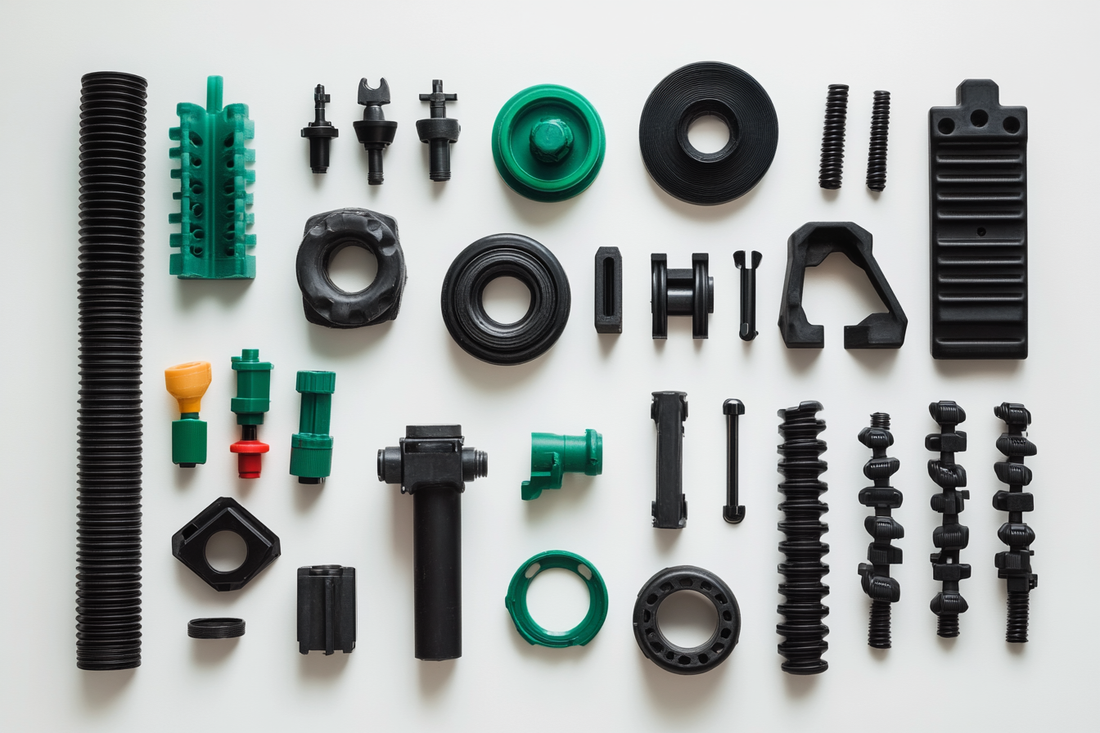
Rubber Injection Molding vs. Compression Molding: A Comprehensive Guide for Custom Rubber Manufacturers
Share
Rubber Injection Molding vs. Compression Molding: A Comprehensive Guide for Custom Rubber Manufacturers
Understanding Rubber Molding Techniques
Custom rubber manufacturers rely on two primary molding processes: rubber injection molding and compression molding. Each technique offers unique advantages for producing molded rubber products with distinct characteristics.
Rubber Injection Molding: Precision Engineering
Process Overview:
- Advanced rubber injection molding technique
- Liquid rubber compound injected under high pressure
- Precise filling of complex mold geometries
Key Advantages:
- Highest precision in molded rubber products
- Rapid production for custom rubber manufacturers
- Minimal material waste
- Consistent part quality
- Ideal for high-volume rubber molding
Optimal Applications:
- Automotive rubber components
- Precision medical device parts
- Complex industrial seals
- High-performance engineering components
Compression Molding: Versatile Rubber Manufacturing
Process Overview:
- Raw rubber material placed in an open mold
- Heated and compressed to create molded rubber products
- Traditional custom rubber manufacturing method
Key Advantages:
- Lower initial tooling costs
- Flexibility in rubber compound selection
- Excellent for specialized rubber product runs
- Adaptable to various rubber material types
Comparative Analysis for Rubber Molding Selection
Injection Molding Recommended When:
- Producing 1000+ molded rubber products
- Requiring extreme precision
- Creating complex rubber component designs
- Minimizing production waste
- Ensuring consistent rubber product quality
Compression Molding Recommended When:
- Developing prototype rubber components
- Working with specialized rubber compounds
- Creating larger, simpler rubber parts
- Managing limited production budgets
- Requiring material flexibility
Key Considerations for Selection
- Production Volume: Injection molding excels at high-volume runs
- Part Complexity: Injection molding handles intricate designs better
- Material Type: Some compounds work better in compression molding
- Cost Constraints: Compression molding offers lower initial tooling expenses
- Tolerance Requirements: Injection molding provides tighter tolerances
Conclusion
The choice between injection and compression molding depends on your specific project requirements. Consulting with experienced custom rubber manufacturers can help determine the most effective approach for your unique application.
Ready to Explore the Right Molding Solution for Your Project? Contact our expert team for personalized manufacturing guidance.